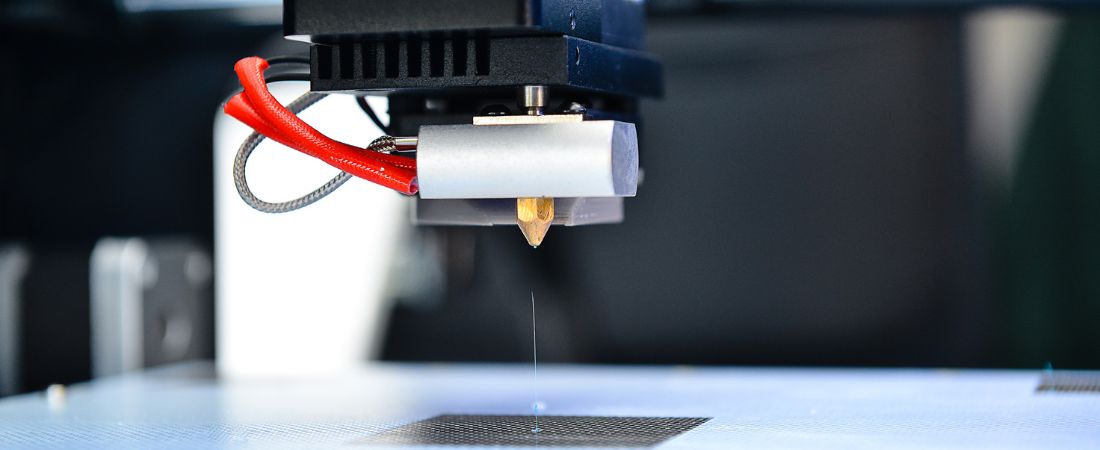
3D printing has become increasingly common in recent years. Every day, there’s news about discoveries, inventions, and developments in the additive manufacturing business, from health to aerospace to design and construction. However, there is still a lot of silence in one business about 3D printing breakthroughs.
We’re discussing the fashion sector here. It’s undeniable that the earliest 3D printed clothes trials and advancements were only recently documented. However, if you have been paying attention to these fashion trends, you may have observed that they are high-end fashion, or apparel designed for the runways and red carpet rather than for everyday use.
The reason why combining 3D printing and clothing appears to be so difficult is straightforward: 3D printing materials, which are largely plastic and metal, are not flexible enough. To address this issue, some fashion and 3D aficionados researched possible solutions and settled on 3D knitwear as the best alternative. But exactly what is 3D knitwear? What makes it different from additive manufacturing and traditional textile production? Will 3D knitwear become widely available as ready-to-wear in the near future? We dug deeper into this topic and answered all these queries with the help of several industry experts.
To comprehend the concept of 3D knitting, as well as its differences and similarities to 3D printing, it is necessary to first review the definitions. 3D printing is the process of computer-controlled machinery manufacturing three-dimensional items layer by layer. The question now is whether 3D knitwear is produced using the same principles. Here is how 3D printing is continuing to move fashion forward.
Production of 3D Knitwear
The production of 3D knitted fabrics is comparable to that of other 3D items. Both start with a computer: CAD software is used to generate the design, and then a programming language is learned. The digital codes are subsequently sent to the machine, which starts the production process. Knitwear and traditional 3D printing are separated by the machine used.
The machine is not a 3D printer that processes filament or powder through extruders, but rather a knitting machine that can manufacture a three-dimensional garment in a single pass by connecting it thread by thread, which is the fundamental difference from additive manufacturing. As a result, it is important to emphasize that while both processes are based on software and are additively created, the material makes a significant difference between them.
As a result, it’s not unexpected that industry experts concur that 3D knitted goods aren’t made using 3D printing, but rather with 3D knitting as a separate technology.
Compared To Conventional Textile Production
After examining the differences and similarities between 3D knitwear and 3D printing, the issue remains if and why 3D knitwear should be favored over traditionally created clothes. Traditional textile production must first be analyzed more closely in order to provide a reasonable solution.
The Major Downside of Conventional Textile Production
With so few corporations keeping their value chains and production practices clear, this is still a delicate subject. In low-cost manufacturing countries, obvious and recurring difficulties such as child labor, low pay, and inadequate protective measures are joined by the industry’s astronomically unfavorable environmental impact. From cotton farming, where pesticides are used and a large amount of water is wasted, to transit, where the material is broken down and exported to another country, this phase alone requires a lot of improvement.
The woven fabric is then returned to another mill to be bleached or colored. The hazardous compounds employed in this procedure are mainly disposed of in wastewater, resulting in pollution of rivers and oceans.
Finally, the garment is stitched, knitted, and completed at a different facility, wasting a significant amount of material in the process. The finished goods are distributed to various locations throughout the world. The extremely long transportation routes, which greatly increase CO2 emissions, balance out the drawbacks of conventionally made clothes. Smaller manufacturers who focus on sustainable, fair, and regional production do exist, but large-scale fashion producers who use traditional production methods continue to dominate the garment market.
Most companies in this field are focused on these social and environmental issues, which is why they all prioritize sustainability in the development of their businesses and the manufacturing of their products. The acquisition of materials is when awareness begins; more than half of all clothing is made from synthetic fibers, such as polyester, nylon, elastane, and acrylic, which are derived from fossil fuels and thus have a negative environmental impact. However, new industrial methods use merino wool, which is sourced sustainably and has a smaller environmental footprint than synthetic fibers.
What Kind of Benefits Could You Expect From 3D-Printed Knitwear?
Because 3D knitwear is made on-demand, issues like overproduction and inventory waste can be avoided. Long supply chains prevent large-scale fashion makers from reacting flexibly and promptly to market changes, resulting in overproduction and overstocking. This is a deadly problem in today’s fast fashion industry, when new collections and items are released almost weekly. And where should the “old” clothes that haven’t been replaced go? These resource- and energy-intensive produced textiles are mainly discarded or partially burned. On-demand, on-site and in-house production could be a viable option here. As a result, not only are transportation costs and emissions reduced, but waste is also virtually eliminated.
3D knitwear can also be personalized thanks to 3D technology. Patterns can readily be adjusted and adapted to customer specifications because the designs are made digitally and every needle stitch is equivalent to a pixel, allowing for a lot of flexibility. Users are obviously open to all innovations and personalizations, with the help of the open-source system and knitting machines. Finally, traditional issues such as worker exploitation through in-house, regional productions are addressed.
We hope you have enjoyed our recap of how 3D printing is continuing to move fashion forward! If you are looking to employ a 3D printing company in New York, be sure to reach out to Tangible Creative today!
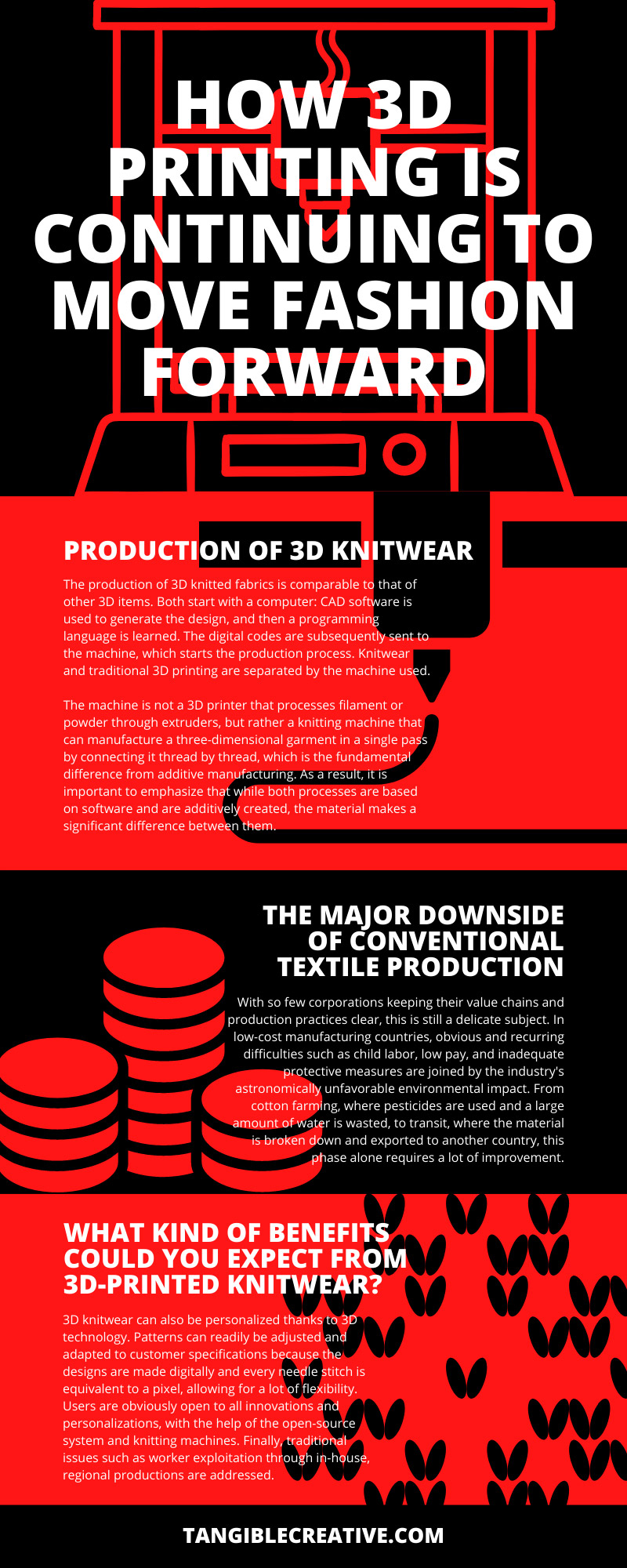