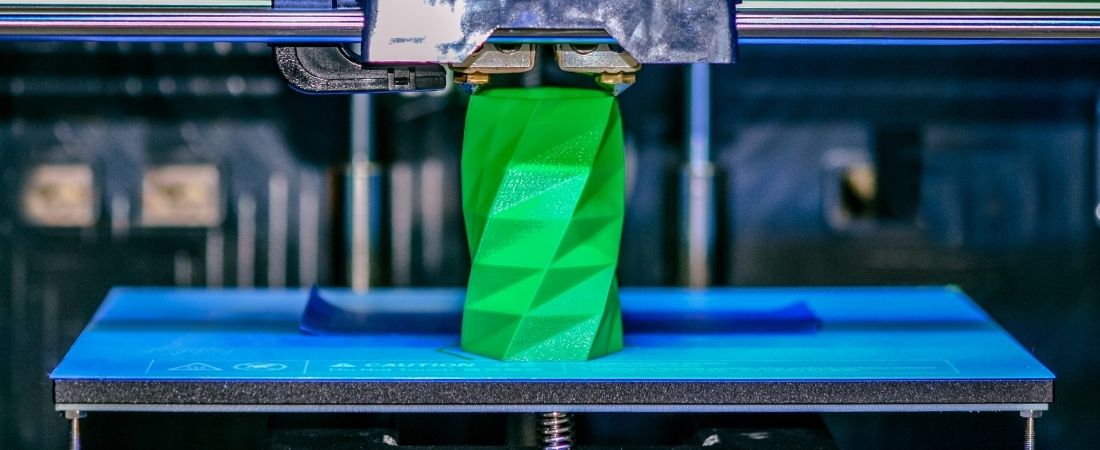
Fused deposition modeling (FDM)—commonly known as fused filament fabrication (FFF)—is an additive manufacturing technique that belongs to the material extrusion category. An object is constructed in FDM when layer by layer selectively deposits melted material in a predefined direction. The materials are thermoplastic polymers that come in the form of filaments.
It’s the most used 3D printing technology and has the world’s largest installed base of 3D printers. It’s frequently the first 3D printing technology that consumers come across. Here is everything you need to know about FDM 3D printing!
How Does FDM Work?
The initial step in the FDM production process is to load a spool of thermoplastic filament into the printer. The filament is fed into the extrusion head and nozzle, where it melts once the nozzle has reached the proper temperature. The extrusion head is connected to a three-axis system that allows it to move in three directions: X, Y, and Z. Melted material is extruded in thin strands and deposited in preset locations, layer by layer, where it cools and hardens. Speed up the cooling process by adding fans to the extrusion head.
Characteristics of FDM 3D Printing
One of the most typical FDM characteristics is warping. The dimension of extruded material shrinks as it cools during solidification. Because the print cools at different rates, the dimensions of different sections change at varying rates.
As demonstrated in Figure 3, differential cooling causes internal tensions to build up, pulling the underlying layer higher and causing it to deform. Close temperature monitoring of the FDM system (namely, the build platform and chamber) and increased adhesion between the part and the build platform can help reduce warping. Warping can also be avoided if you stay clear of wide flat sections and add fillets to sharp corners.
FDM pieces aren’t frequently printed solid to save time and money on printing. Instead, the outer perimeter—known as the shell—is traced in multiple passes, and the interior—known as the infill—is filled with a low-density internal structure.
FDM Best Practices
When you are working with FDM printing, it is important to keep the following in mind:
- FDM is capable of producing prototypes and working parts in a timely and cost-effective manner.
- FDM materials come in a variety of shapes and sizes.
- A desktop FDM 3D printer’s typical construction size is 200 x 200 x 200mm. The build size of industrial machines is greater.
- Because FDM is anisotropic by nature, it is inappropriate for mechanically demanding components.
We hope this article has told you everything you need to know about FDM 3D printing! If you are looking for an FDM 3D printing service, reach out to Tangible Creative for amazing craftsmanship and great turnaround times!