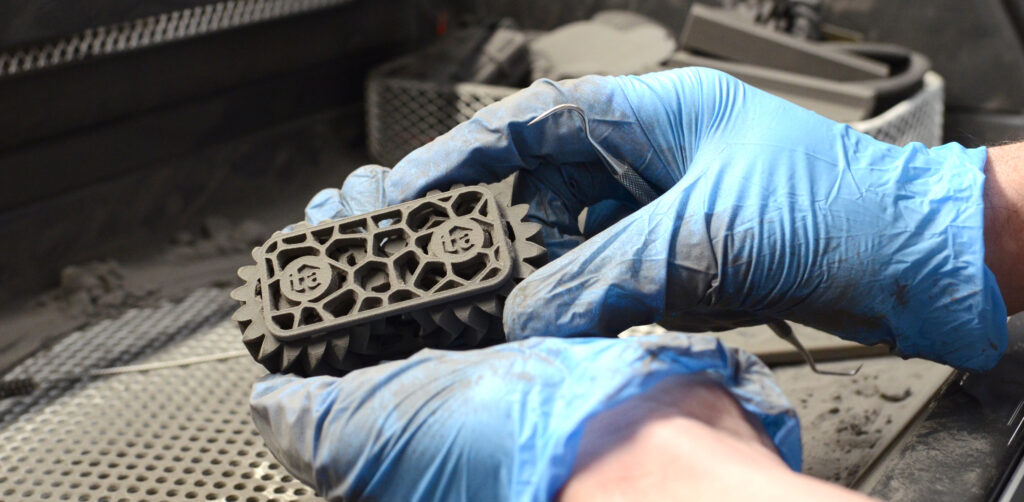
SLS 3D printing is the newest type of 3D printing to be found in the 3D printing landscape. This type of printing uses nylon plastic powder and polymer filaments to craft extremely accurate and well-finished models made out of different types of plastics. Most commonly used for SLS 3D printing is nylon 11 and 12, with a high heat deflection temperature, as compared to other methods of 3D printing. While this may seem like a simple process, it is actually a highly complex process that takes many hours of experience to perfect. As such, this type of 3D printing is often used in end-stage production runs as proof of concept, with polymer FDM 3D printing taking up the majority of the beginning parts of production.
Read on to learn more about the materials used in SLS 3D printing.
What Is SLS 3D Printing?
SLS 3D printing, also known as the process of selective laser sintering, is a manufacturing technique that utilizes laser sintering technology and plastic nylon powder or filaments to form a final product. This process starts with a machine depositing powdered plastic filaments in layers on a chamber bed and alternating between depositing them and sintering them to the lower layer, much like fused deposition modeling. After this, the first part of the modeling process is complete, and the model has been formed. The printer now takes this semi-finished product, and puts it in a vacuuming area where the spare particles of SLS nylon powder are removed from the solid piece, in order for the 3D sintered object that the SLS printer has created can be revealed. The spare particles are then collected from the vacuuming area, and are return into the larger chamber where the objects were initially 3D printed. The powder is ready for reuse. The chamber is then placed back into the SLS 3D printing machine and the nylon powder is then compressed. This circular reuse of materials makes SLS 3D printing one of the most sustainable forms of additive manufacturing around, since all the materials are recycled until their final use and when the loose powder takes formation.
After the print has been removed of all excess SLS nylon powder, either by hand or vacuuming methods it is now complete and takes a solid shape. The SLS 3D printed object can be finished, painted and fabricated appropriately.
What Uses Does SLS 3D Printing Have?
SLS 3D printing has many different uses in many different types of manufacturing areas. For one, the fact that you can make a full-scale plastic model in one piece, with moving parts, of nearly anything is essential for many industries, such as automotive and aerospace manufacturing. Furthermore, this type of printing can print to tight tolerance, meaning the specificity of the measurements you output will be exact. Besides this, one of the biggest upsides to this type of printing is the turnaround time. With this type of technology, you can print an object in very little time compared to the manufacturing times of the past.
What Materials Are Used in SLS 3D Printing?
As it turns out, there are many different types of materials that are used in this type of 3D printing. In fact, you can order many different materials, ranging from nylon, polyamides (PA), polystyrenes (PS), thermoplastic elastomers (TPE), and polyaryletherketones (PAEK). Most commonly used in SLS printing is nylon powder, to fit whatever needs your project may require. Furthermore, this type of printing is exceptional for middle- to end-stage manufacturing techniques, meaning it is even viable for small businesses in the modeling or design industry. If you really wanted to, you could even set up an automated design center for SLS 3D printing for an online business.
We hope you have enjoyed our quick overview of the materials used in SLS 3D printing. If you are looking to utilize an SLS 3D printing company, be sure to reach out to Tangible Creative today!